Claudia Flavell-Mens profiler verden-endre innsats av Fritz Haber og Carl Bosch
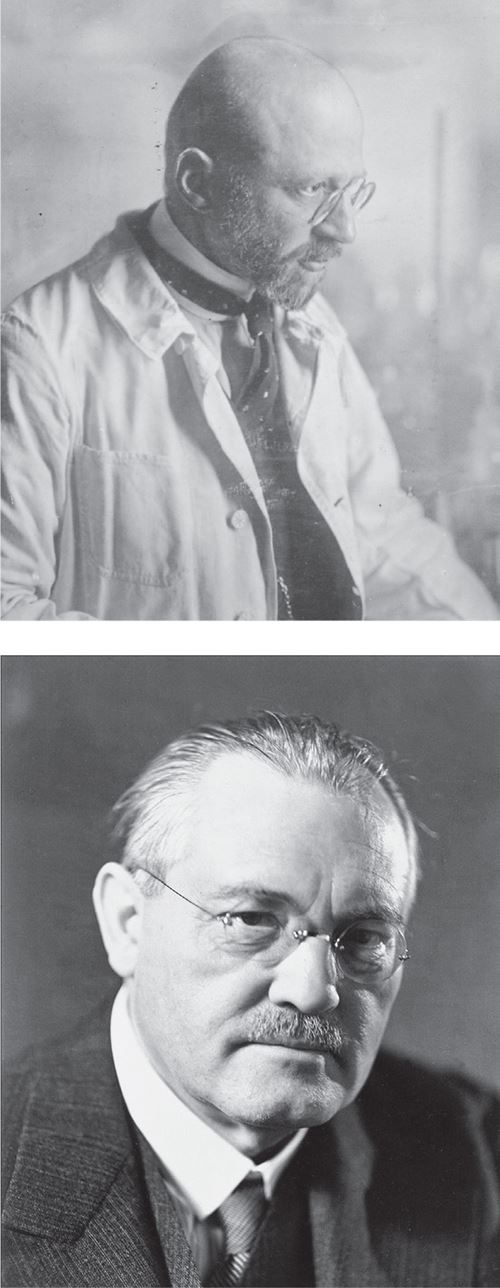
Ingen kjemisk prosessteknologi prestasjon bedre illustrerer tveegget arten av mange oppfinnelser enn Haber-Bosch-prosessen., Utviklet av industrielle apoteker Fritz Haber og skaleres opp av kjemisk ingeniør Carl Bosch, de Haber-Bosch-prosessen tar nitrogen fra luften og konverterer det til ammoniakk.
Dette har gjort det mulig for første gang å produsere syntetisk gjødsel og produsere nok mat til verdens voksende befolkning. Faktisk, uten Haber-Bosch-prosessen vi ville bare være i stand til å produsere rundt to tredjedeler mengden mat vi gjør i dag, og Jordens ville befolkningen ha for å minske tilsvarende.,
På baksiden, nitrogen er også et viktig råstoff i produksjon av høy eksplosiver. Når Tyskland uttømt sine forsyninger av naturlige ammoniakk i de tidlige stadier av første Verdenskrig, syntetiske ammoniakk var der for å fylle gapet. Uten Haber-Bosch-prosessen Verdenskrig, ville jeg ha blitt vesentlig kortere.
Haber, en consummate patriot, som senere skulle få beryktet gjennom sitt arbeid med kjemikalier for å Tysklands fordel i første Verdenskrig, og han personlig tilsyn og regissert den første store utslipp av klor gass i Ypres i 1915.,
Avverge sult
Likevel, det er Haber-Bosch-prosessen og dens bidrag til å fø verdens voksende befolkning som han er mest kjent for, og det med rette. Med framveksten av den industrielle tidsalder og den store flytte til byene, gjødsel var avgjørende for topping opp jord med næringsstoffer. Naturlig gjødsel, for eksempel Chilenske guano var en begrenset ressurs – hvis vitenskapen ikke kom til unnsetning, hungersnød var sikker på å følge.
Løse problemet tjent Haber og Bosch to nobelpriser i kjemi: Haber i 1918, Bosch i 1931.,
problemet med nitrogen er at mens det er rikelig i atmosfæren, sin trippel obligasjoner gjøre nitrogen molekylet utrolig stabil og derfor vanskelig å fastsette. Haber var en av en gruppe kjemikere som også inkluderte Walther Nernst og Henry Le Chatelier, som hadde bestemt seg for å takle problemet.,
Uten Haber-Bosch-prosessen vi ville bare være i stand til å produsere rundt to tredjedeler mengden mat vi gjør i dag
Trasé og villspor
Haber i utgangspunktet forsøkt å lage nitrogenoksid med hjelp av elektriske utladninger, etterligne naturlige prosesser i tordenvær. Men utbyttet var så lav, og prosessen så byrdefull at Haber avvist det som upraktisk.
Haber neste undersøkt høy temperatur syntese, med en viss suksess, og selv lyktes i å produsere en liten mengde av nitrogen i 1905., Men han var skuffet med 5% rente, ved temperaturer på rundt 1000ºC. Bedre katalysatorer eller høyere press var nødvendig, men høyt trykk syntese var i sin spede begynnelse og egnet utstyr knappe. Faktisk, Le Chatelier, som var den første til å foreslå å fikse nitrogen under høyt trykk, ga opp etter en spesielt heftig laboratorium eksplosjon.
Det var ikke før i 1908 at Haber, arbeider med sin student Robert le Rossignol, bestemte oss for å takle høyt trykk rute. Det var et godt valg., Ett år på, de patentert en prosess som ga noen 15% ammoniakk, drift ved et trykk på ca 175 atmosfærer på 550ºC over en osmium og uran katalysator.
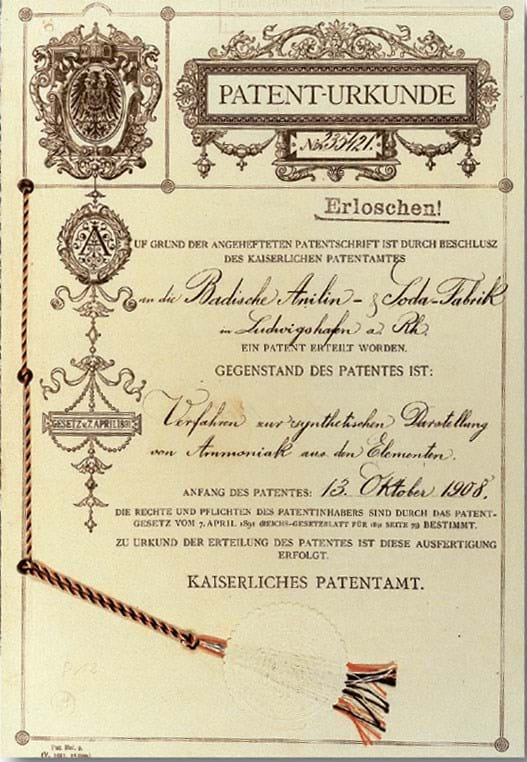
Fra lab til industrien
prosessen ble snart tildelt Badische Anilin und Soda Fabrik (bedre kjent i dag av sin forkortelse, BASF), som har fått i oppgave kjemisk ingeniør Carl Bosch med skalering opp prosessen., Bosch sa senere: «Det var tydelig at det var tre viktigste problemene som måtte nødvendigvis være avgjort før bygging av et anlegg kan iverksettes. Disse var i tilførsel av råstoff, dvs. av gassene hydrogen og nitrogen, til en lavere pris enn hittil mulig; produksjon av effektive og stabile katalysatorer; og til slutt bygging av apparatet.,»
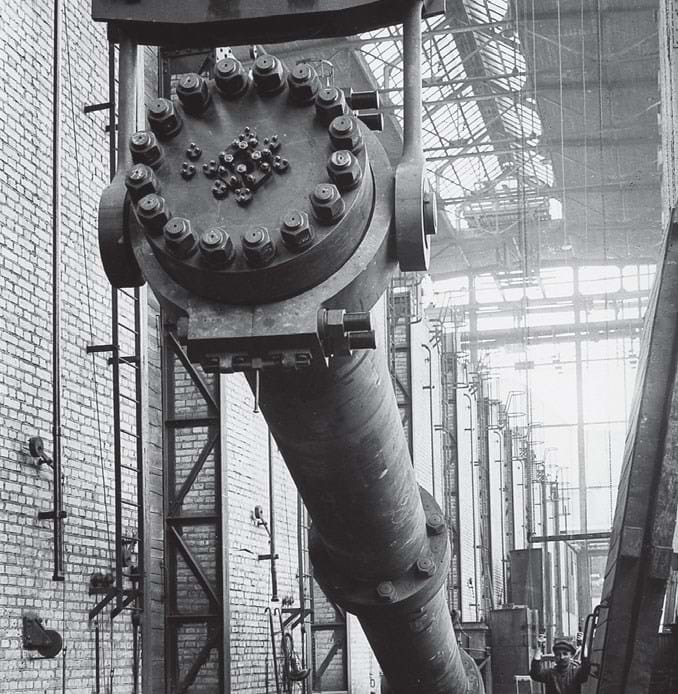
Billig og munter
Haber er prosessen med å produsere hydrogen via elektrolyse ikke egner seg til å skalere opp. Det gjorde heller ikke noen av de andre kjente hydrogen produksjon prosesser, som var enten for dyrt eller produsert hydrogen med for mange urenheter.
Bosch og hans team til slutt slo seg ned på vann-gass – en syntese gass som består av hydrogen og karbonmonoksid – som den eneste praktiske løsningen., Selskapet hentet ren hydrogen ved hjelp av nyutviklet Linde-Frank-Caro-prosessen, som kjøler ned vann gass i flere trinn til-205ºC, der alle elementer bortsett fra hydrogen kondensere.
Den andre store bidrag var å erstatte uran osmium katalysator med en mer praktisk alternativ. Osmium var uegnet for skalere opp fordi global leverer utgjorde bare noen få kilogrammes, og uran var dyrt og svært følsomme for vann og oksygen. Det tok Bosch assistent, kjemiker Alwin Mittasch, rundt 20.000 eksperimenter for å perfeksjonere en blandet katalysator basert på jernoksid., Det var det første av sitt slag, og utføres så vel som osmium og uran, og var lett tilgjengelig og billig. Katalysator er fortsatt i bruk i dag, og Mittasch er husket som en av de store pionerene av katalytisk kjemi.
trykkbeholdere
Bosch mener hans største prestasjon var å løse det tredje problemet, hvordan å bygge en reaktor som ville tåler både høye temperaturer og høyt trykk av reaksjonen. Høyt trykk kjemi fortsatt var et helt nytt felt, og egnet utstyr var mangelvare., Den eneste eksisterende høy-press-prosessen var Linde air lng (liquefied natural gas prosess, en lav-temperatur prosess som brukte en myk loddet kobber reaktoren som var helt uegnet for høy temperatur.
Bosch ‘ s første oppgave var å utarbeide et nytt laboratorium på kjeller, som han re-modellert Haber opprinnelige design inn i en robust, pålitelig reaktoren. 24 eksempler løp døgnet rundt i flere år mens Mittasch søkte etter den perfekte katalysatoren.,
Den lille reaksjon kamre hadde ingen problemer med Bosch var å møte i skala-up: ytre press-bærende deler som var liten nok til at luft kjøling var tilstrekkelig til å holde dem stabile, og det var bare en liten mekanisk stress på de indre delene.
«Som en tilstand ble snart til å endre seg når vi begynte å bygge en mindre converter som en produksjon apparater,» Bosch sa. Når Haber hadde gjort en lignende forsøk, enheten mislyktes etter bare et par timer etter operasjonen, så Bosch ‘ s team utviklet en veldig solid, eksternt-oppvarmet kontakt tube som en reaksjon på kammeret., Selv så, tok de ingen sjanser: «å Være forsiktige, vi hadde plassert det i en sterk, armert betong kammer langt bort fra den travle sentre for aktivitet på siden i mellomtiden hadde vi også blitt kjent med faren for brann og flarebacks som oppstår, ofte med spontan tenning, når hydrogen kommer ut ved høyt trykk,» sa han.
Det var en klok forholdsregel: etter 80 timer av tjenesten, materialet ble sprø og rør sprekker. Det viste seg at hydrogen hadde decarbonised den perlite i karbon stål og dannet en sprø legering med jern.,
Bosch løst problemet ved å utvikle den første foret reaksjonskammeret – en trykk-bærende stål tynt foret med et mykt stål. Hydrogen var i stand til å spre seg gjennom fôr og fikk lov til å flykte gjennom spor og hull i jakken, for å hindre en farlig trykkoppbygging.
«løsningen dukket opp enkle og var faktisk slik, men likevel hele utviklingen av den prosessen er avhengig av den til en større eller mindre grad,» Bosch sa.,
Sikkerhetsmessige hensyn
Ikke at dette var den siste av Bosch er problemer: varmeveksler var for lite, press-bærende stål jakker fortsatt en tendens til å spenne og eksplodere etter langvarig drift – et problem bare overvinne da Bosch, i strid med konvensjonen av ganger, prøvde oppvarming reaktoren fra innsiden – og kompressorer som var upålitelig og hadde en tendens til å lekke. Denne utgjør en uakseptabel risiko når gassen lekker ut er hydrogen, for ikke å nevne at ingen kjemiske anlegg kan arbeide med kompressorer som ikke minst en gang om dagen.,
Bosch ‘ s team ikke bare bygget sin egen kompressorer, det hadde også til å designe og produsere sin egen overvåking av instrumenter for å måle temperatur, intensitet av gasstrøm og sammensetningen av gassen i reaksjonskammeret – off-the-sokkel enheter 20 år på, men uhørt når Bosch skalert opp Haber enhet.
Bosch var også veldig bevisst på helse og sikkerhet, og designet en rekke hurtigvirkende sikkerhet ventiler og annet utstyr, slik at anlegget kan bli stengt og evakuert med rekordfart., «Gjennom årene har vi vært i stand til å samle tilstrekkelig erfaring, spesielt under krigen når Oppau verker ble bombet natt etter natt, og vi er fortsatt av den oppfatning i dag at man ikke kan være for forsiktig,» sa han.
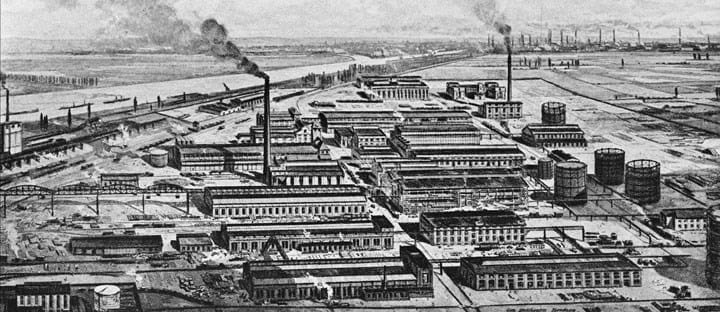
Naturen vet best
Det første anlegget for å bruke Haber-Bosch-prosessen i industriell skala startet opp i BASF Oppau i 1913. I nesten 100 år, om ikke mye har endret seg, og prosessen er fortsatt i bruk rundt om i verden.,
Imidlertid Haber spådd at dette vil endre: «Nitrogen bakterier, lærer oss at Naturen, med sin sofistikerte former for kjemi av levende materie, likevel forstår og tar i bruk metoder som vi ikke ennå vet hvordan å imitere. La det være nok at i mellomtiden forbedret nitrogen gjødsling av jorden bringer nye nutritive rikdom til menneskeheten, og at den kjemiske industrien kommer til unnsetning bonde som, i den gode jorden, endringer steiner om til brød.»
som Opprinnelig ble publisert i Mars 2010
Legg igjen en kommentar