Claudia Flavell-tout en profils les efforts de changement du monde de Fritz Haber et Carl Bosch
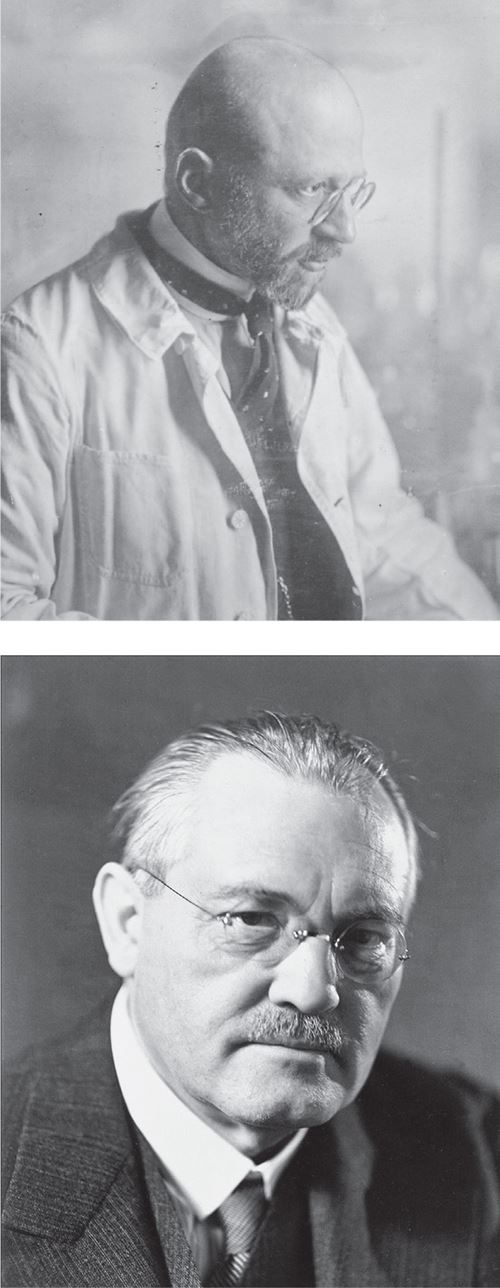
aucune prouesse en Génie Chimique n’illustre mieux la nature à double tranchant de nombreuses inventions que le procédé Haber-Bosch., Développé par le chimiste industriel Fritz Haber et mis à l’échelle par L’ingénieur chimiste Carl Bosch, Le procédé Haber-Bosch prend l’azote de l’air et le convertit en ammoniac.
cela a permis pour la première fois de produire des engrais synthétiques et de produire suffisamment de nourriture pour la population croissante de la Terre. En effet, sans le processus Haber-Bosch, nous ne serions en mesure de produire environ les deux tiers de la quantité de nourriture que nous faisons aujourd’hui, et la population de la Terre devrait diminuer en conséquence.,
d’un autre côté, l’azote est également une matière première clé dans la production d’explosifs à haute teneur. Lorsque L’Allemagne a épuisé ses réserves d’ammoniac naturel au début de la Première Guerre mondiale, l’ammoniac synthétique était là pour combler le vide. Sans le processus Haber-Bosch, La Première Guerre mondiale aurait été considérablement plus courte.
Haber, un patriote accompli, gagnera plus tard en notoriété grâce à ses travaux sur l’utilisation de produits chimiques à l’avantage de l’Allemagne pendant la Première Guerre mondiale, et il supervisera et dirigera personnellement la première libération à grande échelle de chlore gazeux à Ypres en 1915.,
éviter la famine
néanmoins, C’est le processus Haber-Bosch et sa contribution à l’alimentation de la population mondiale croissante qui lui est le mieux connu, et à juste titre. Avec l’avènement de l’ère industrielle et le grand déménagement vers les villes, les engrais étaient essentiels pour remplir le sol en nutriments. Les engrais naturels tels que le guano Chilien étaient une ressource limitée – si la science ne venait pas à la rescousse, la famine allait certainement suivre.
la résolution du problème a valu à Haber et Bosch deux prix Nobel de chimie: Haber en 1918, Bosch en 1931.,
le problème avec l’azote est que, bien qu’il soit abondant dans l’atmosphère, ses liaisons triples rendent la molécule d’azote incroyablement stable et donc difficile à fixer. Haber faisait partie d’un groupe de chimistes qui comprenait également Walther Nernst et Henry Le Chatelier, qui avaient décidé de s’attaquer au problème.,
sans le procédé Haber-Bosch, nous ne serions en mesure de produire environ les deux tiers de la quantité de nourriture que nous faisons aujourd’hui
voies et ruelles aveugles
Haber a d’abord tenté de produire de l’oxyde nitrique à Mais le rendement était si faible et le processus si onéreux que Haber l’a rejeté comme peu pratique.
Haber a ensuite étudié la synthèse à haute température, avec un certain succès, et a même réussi à produire une petite quantité d’azote en 1905., Mais il a été déçu par le rendement de 5%, à des températures d’environ 1000ºC. De meilleurs catalyseurs ou une pression plus élevée étaient nécessaires, mais la synthèse à haute pression en était à ses débuts et les équipements appropriés étaient rares. En effet, Le Chatelier, qui a été le premier à suggérer de fixer l’azote sous haute pression, a renoncé après une explosion de laboratoire particulièrement lourde.
Ce n’est qu’en 1908 que Haber, en collaboration avec son élève Robert Le Rossignol, décide de s’attaquer à la voie haute pression. C’était un bon choix., Un an plus tard, ils ont breveté un procédé qui a produit environ 15% d’ammoniac, fonctionnant à une pression d’environ 175 atmosphères à 550ºC sur un catalyseur à l’osmium et à l’uranium.
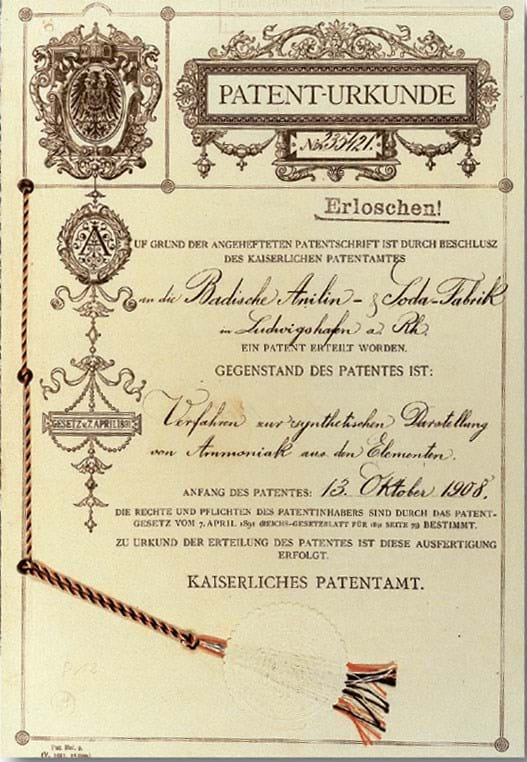
du laboratoire à l’industrie
Le procédé a rapidement été attribué à Badische Anilin und Soda Fabrik (plus connu aujourd’hui sous son abréviation, BASF), qui a chargé L’ingénieur chimiste Carl Bosch., Bosch a déclaré plus tard: « il était évident qu’il y avait trois problèmes principaux qui devaient nécessairement être réglés avant que la construction d’une usine puisse être entreprise. Il s’agissait de la fourniture de matières premières, c’est-à-dire des gaz hydrogène et azote, à un prix inférieur à ce qui était jusqu’à présent possible; la fabrication de catalyseurs efficaces et stables; et enfin la construction de l’appareil., »
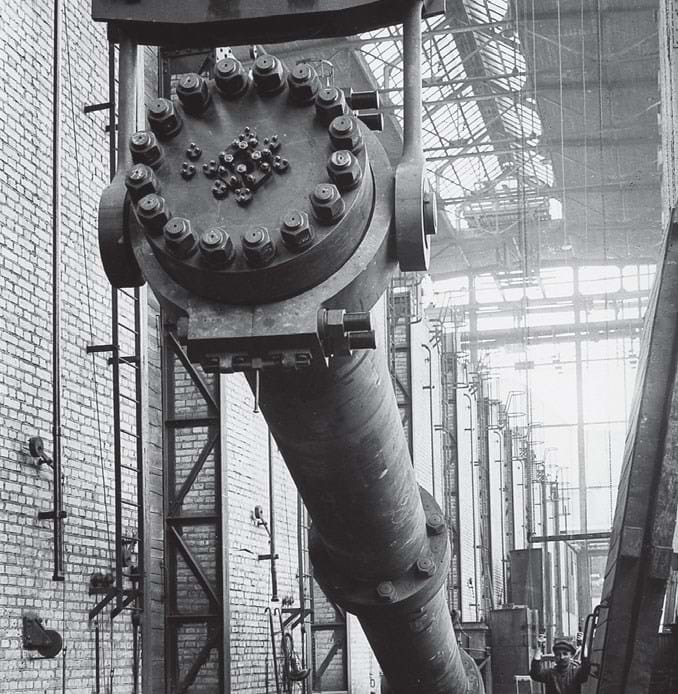
bon marché et joyeux
le processus de production D’hydrogène par électrolyse de Haber ne se prêtait pas à la mise à l’échelle. Aucun des autres procédés de production d’hydrogène connus, qui étaient soit trop coûteux, soit produisaient de l’hydrogène avec trop d’impuretés, ne l’était non plus.
Bosch et son équipe ont finalement opté pour l’eau-gaz – un gaz de synthèse composé d’hydrogène et de monoxyde de carbone – comme seule solution pratique., La société a extrait de l’hydrogène pur en utilisant le procédé Linde-Frank-Caro récemment développé, qui refroidit le gaz de l’eau en plusieurs étapes jusqu’à-205ºC, auquel moment tous les éléments à l’exception de l’hydrogène se liquéfient.
la deuxième contribution majeure a été de remplacer le catalyseur uranium-osmium par une alternative plus pratique. L’Osmium a été impropre à l’échelle mondiale parce que les fournitures s’élève à seulement quelques kilogrammes, et de l’uranium a été coûteux et très sensible à l’eau et à l’oxygène. Il a fallu à L’assistant de Bosch, le chimiste Alwin Mittasch, quelque 20 000 expériences pour perfectionner un catalyseur mixte à base d’oxyde de fer., Il était le premier de son genre, et exécuté aussi bien que l’osmium et l’uranium, et était facilement disponible et bon marché. Le catalyseur est toujours utilisé aujourd’hui et Mittasch est considéré comme l’un des grands pionniers de la chimie catalytique.
récipients sous pression
Bosch pense que son plus grand exploit a été de résoudre le troisième problème, comment construire un réacteur qui résisterait à la fois aux hautes températures et aux hautes pressions de la réaction. La chimie à haute pression était encore un domaine très nouveau et les équipements appropriés étaient rares., Le seul procédé à haute pression existant était le procédé de liquéfaction de L’air de Linde, un procédé à basse température utilisant un réacteur en cuivre soudé souple qui ne convenait absolument pas aux applications à haute température.
la première tâche de Bosch a été de concevoir un nouveau réacteur de laboratoire, pour lequel il a remodelé la conception originale de Haber en un réacteur robuste et fiable. Certains exemples 24 ont fonctionné 24 heures sur 24 pendant plusieurs années, tandis que Mittasch cherchait le catalyseur parfait.,
Les petites chambres de réaction n’avaient aucun des problèmes que Bosch devait rencontrer lors de la mise à l’échelle: les pièces extérieures à pression étaient suffisamment petites pour que le refroidissement à l’air soit suffisant pour les maintenir stables, et il n’y avait que de légères contraintes mécaniques sur les pièces intérieures.
« cet état de choses allait bientôt changer lorsque nous avons commencé à construire un convertisseur plus petit en tant qu’appareil de production”, a déclaré Bosch. Lorsque Haber avait fait une tentative similaire, l’appareil a échoué après seulement quelques heures de fonctionnement, de sorte que L’équipe de Bosch a conçu un tube de contact très robuste, chauffé à l’extérieur comme chambre de réaction., Malgré tout, ils n’ont pris aucun risque: « en faisant preuve de prudence, nous l’avions logé dans une chambre solide en béton armé, loin de tous les centres d’activité occupés, car entre-temps, nous avions également pris connaissance du danger des incendies et des éruptions qui se produisent, souvent avec inflammation spontanée, lorsque l’hydrogène émerge à haute pression”, a-t-il déclaré.
c’était une sage précaution: après 80 heures de service, le matériau devenait fragile et les tubes éclataient. Il s’est avéré que l’hydrogène avait décarboné la perlite dans l’acier au carbone et formé un alliage fragile avec le fer.,
Bosch a résolu le problème en concevant la première chambre de réaction doublée – une chemise en acier à palier de pression finement doublée d’un acier souple. L’hydrogène a pu diffuser à travers la doublure et a été autorisé à s’échapper à travers les rainures et les trous de la veste, pour éviter une accumulation de pression dangereuse.
« la solution semblait simple et l’était en fait, mais pourtant tout le développement du processus en dépendait plus ou moins”, a déclaré Bosch.,
considérations de sécurité
Ce n’était pas le dernier des problèmes de Bosch: l’échangeur de chaleur était trop inefficace, les gaines en acier à pression tendaient encore à se boucler et à exploser après un fonctionnement prolongé-problème que Bosch, En rupture avec les conventions de l’époque, essayait de chauffer le réacteur de l’intérieur – et des compresseurs peu fiables et tendaient à fuir. Cela pose un risque inacceptable lorsque le gaz qui s’échappe est de l’hydrogène; sans oublier qu’aucune usine chimique ne peut fonctionner avec des compresseurs qui tombent en panne au moins une fois par jour.,
L’équipe de Bosch a non seulement construit ses propres compresseurs, mais elle a également dû concevoir et produire ses propres instruments de surveillance pour mesurer la température, l’intensité du flux de gaz et la composition du gaz dans la chambre de réaction – des dispositifs prêts à l’emploi 20 ans plus tard, mais du jamais vu lorsque Bosch a
Bosch était également très conscient de la santé et de la sécurité, et a conçu de nombreuses soupapes de sécurité à action rapide et d’autres équipements afin que l’usine puisse être arrêtée et évacuée à une vitesse record., « Au fil des ans, nous avons pu acquérir une expérience suffisante, en particulier pendant la guerre lorsque les usines D’Oppau ont été bombardées nuit après nuit, et nous sommes toujours d’avis aujourd’hui qu’on ne peut pas être trop prudent”, a-t-il déclaré.
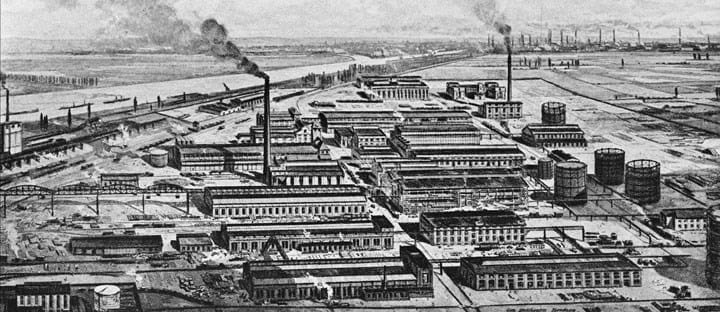
la Nature sait mieux
La première à utiliser le procédé Haber-Bosch à l’échelle industrielle a commencé à BASF Oppau en 1913. Près de 100 ans plus tard, rien n’a changé, et le processus est toujours utilisé dans le monde entier.,
cependant, Haber prédit que cela changerait: « les bactéries azotées nous apprennent que la Nature, avec ses formes sophistiquées de la chimie de la matière vivante, comprend et utilise encore des méthodes que nous ne savons pas encore imiter. Qu’il suffise qu’entre-temps une meilleure fertilisation azotée du sol apporte de nouvelles richesses nutritives à l’humanité et que l’industrie chimique Vienne en aide à l’agriculteur qui, dans la bonne terre, transforme les pierres en pain.”
Initialement publié en Mars 2010,
Laisser un commentaire