Claudia Flavell-Während Profile der weltverändernden Bemühungen von Fritz Haber und Carl Bosch
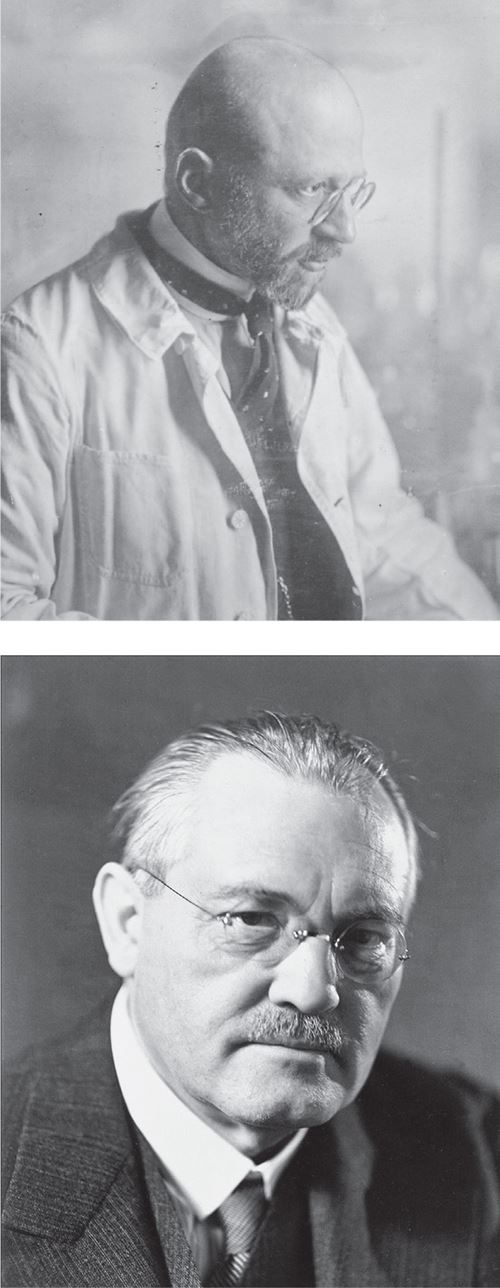
Kein Chemieingenieurwesen veranschaulicht besser den zweischneidigen Charakter vieler Erfindungen als das Haber-Bosch-Verfahren., Das von Industriechemiker Fritz Haber entwickelte und vom Chemieingenieur Carl Bosch skalierte Haber-Bosch-Verfahren entnimmt der Luft Stickstoff und wandelt es in Ammoniak um.
Damit war es erstmals möglich, synthetische Düngemittel herzustellen und ausreichend Nahrung für die wachsende Bevölkerung der Erde zu produzieren. Ohne das Haber-Bosch-Verfahren könnten wir nämlich nur rund zwei Drittel der heutigen Nahrungsmittel produzieren, und die Erdbevölkerung müsste entsprechend schrumpfen.,
Auf der anderen Seite ist Stickstoff auch ein wichtiger Rohstoff bei der Herstellung von Hochsprengstoffen. Als Deutschland in den frühen Stadien des Ersten Weltkriegs seine Vorräte an natürlichem Ammoniak erschöpfte, war synthetisches Ammoniak da, um die Lücke zu füllen. Ohne den Haber-Bosch-Prozess wäre der Erste Weltkrieg deutlich kürzer ausgefallen.
Haber, ein vollendeter Patriot, erlangte später durch seine Arbeit über den Einsatz von Chemikalien zum Vorteil Deutschlands im Ersten Weltkrieg Bekanntheit, und er überwachte und leitete persönlich die erste großflächige Freisetzung von Chlorgas in Ypern in 1915.,
Hungersnot abwenden
Dennoch ist es der Haber-Bosch-Prozess und sein Beitrag zur Ernährung der wachsenden Weltbevölkerung, an den er sich am besten erinnert, und das zu Recht. Mit dem Aufkommen des Industriezeitalters und dem großen Umzug in die Städte waren Dünger unerlässlich, um den Boden mit Nährstoffen aufzufüllen. Natürliche Düngemittel wie der chilenische Guano waren eine begrenzte Ressource – wenn die Wissenschaft nicht zur Rettung kam, würde mit Sicherheit eine Hungersnot folgen.
Die Lösung des Problems brachte Haber und Bosch zwei Nobelpreise für Chemie ein: Haber 1918, Bosch 1931.,
Das Problem mit Stickstoff ist, dass, während es in der Atmosphäre reichlich vorhanden ist, seine Dreifachbindungen das Stickstoffmolekül unglaublich stabil und daher schwer zu fixieren machen. Haber gehörte zu einer Gruppe von Chemikern, zu denen auch Walther Nernst und Henry Le Chatelier gehörten, die beschlossen hatten, das Problem anzugehen.,
Ohne das Haber-Bosch-Verfahren wären wir nur in der Lage, rund zwei Drittel der heutigen Lebensmittel zu produzieren
Wege und Sackgassen
Haber versuchte zunächst, mit Hilfe elektrischer Entladungen Stickstoffmonoxid zu erzeugen, das natürliche Prozesse während eines Gewitters nachahmt. Aber die Ausbeute war so gering und der Prozess so belastend, dass Haber es als unpraktisch abgetan.
Haberl untersuchte die Hochtemperatursynthese mit einigem Erfolg und schaffte es 1905 sogar, eine kleine Menge Stickstoff zu produzieren., Aber er war enttäuscht von der 5% Ausbeute bei Temperaturen von rund 1000ºC. Bessere Katalysatoren oder höherer Druck waren erforderlich, aber die Hochdrucksynthese steckte in den Kinderschuhen und geeignete Geräte waren knapp. In der Tat gab Le Chatelier, der als erster vorschlug, Stickstoff unter hohem Druck zu fixieren, nach einer besonders heftigen Laborexplosion auf.
Erst 1908 entschloss sich Haber zusammen mit seinem Schüler Robert le Rossignol, die Hochdruckroute anzugehen. Es war eine gute Wahl., Ein Jahr später patentierten sie ein Verfahren, das etwa 15% Ammoniak lieferte und bei einem Druck von etwa 175 Atmosphären bei 550ºC über einem Osmium-und Urankatalysator arbeitete.
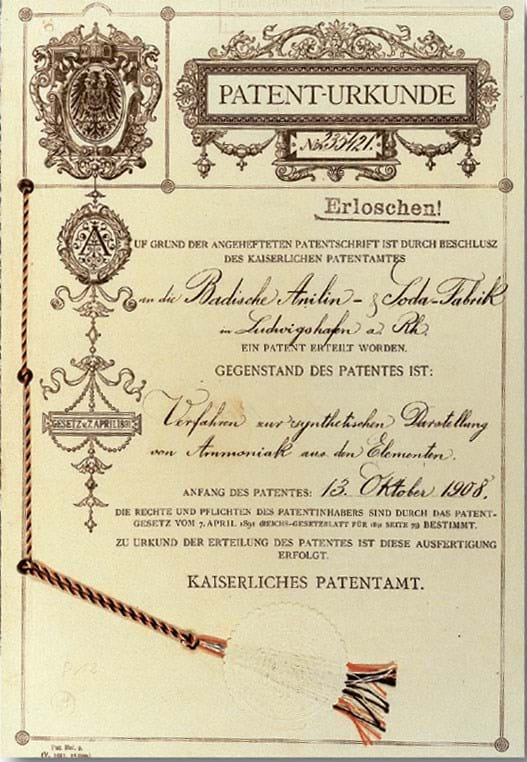
Von Labor zu Industrie
Das Verfahren wurde bald der Badischen Anilin und Soda Fabrik (heute besser bekannt unter der Abkürzung BASF) zugewiesen, die den Chemieingenieur Carl Bosch mit der Skalierung des Prozesses beauftragte., Bosch sagte später: „Es war offensichtlich, dass es drei Hauptprobleme gab, die unbedingt gelöst werden mussten, bevor der Bau einer Anlage durchgeführt werden konnte. Dies waren die Lieferung von Rohstoffen, d. h. der Gase Wasserstoff und Stickstoff, zu einem niedrigeren Preis als bisher möglich; die Herstellung effektiver und stabiler Katalysatoren; und schließlich der Bau der Vorrichtung.,“
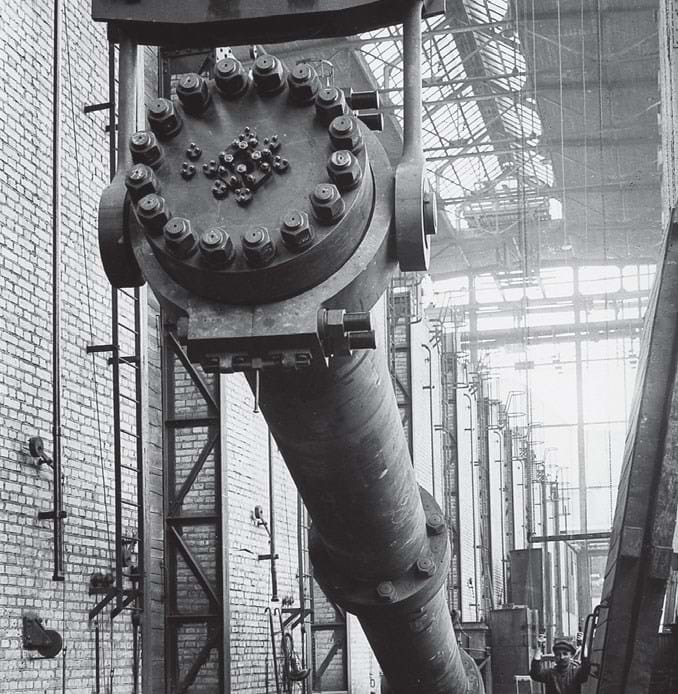
Billig und fröhlich
Habers Prozess der Wasserstofferzeugung über Elektrolyse war nicht skalierbar. Ebenso wenig wie die anderen bekannten Wasserstoffproduktionsprozesse, die entweder zu teuer waren oder Wasserstoff mit zu vielen Verunreinigungen produzierten.
Bosch und sein Team entschieden sich schließlich für Wassergas – ein Synthesegas aus Wasserstoff und Kohlenmonoxid – als einzig praktische Lösung., Das Unternehmen extrahierte reinen Wasserstoff mit dem kürzlich entwickelten Linde-Frank-Caro-Verfahren, das Wassergas in mehreren Schritten auf-205ºC kühlt, wobei alle Elemente außer Wasserstoff verflüssigt werden.
Der zweite große Beitrag bestand darin, den Uran-Osmium-Katalysator durch eine praktischere Alternative zu ersetzen. Osmium war für die Skalierung ungeeignet, da die globale Versorgung nur wenige Kilogramm betrug und Uran teuer und sehr empfindlich gegenüber Wasser und Sauerstoff war. Um einen gemischten Katalysator auf Eisenoxidbasis zu perfektionieren, benötigte Bosch-Assistent, Chemiker Alwin Mittasch, rund 20.000 Experimente., Es war das erste seiner Art, und durchgeführt sowie Osmium und Uran, und war leicht verfügbar und billig. Der Katalysator ist heute noch im Einsatz und Mittasch gilt als einer der großen Pioniere der katalytischen Chemie.
Druckbehälter
Bosch glaubt, dass seine größte Leistung darin bestand, das dritte Problem zu lösen, wie man einen Reaktor baut, der sowohl den hohen Temperaturen als auch den hohen Drücken der Reaktion standhält. Die Hochdruckchemie war noch ein sehr neues Feld, und geeignete Ausrüstung war knapp., Das einzige bestehende Hochdruckverfahren war das Luftverflüssigungsverfahren von Linde, ein Niedertemperatur-Verfahren, bei dem ein weich gelöteter Kupferreaktor verwendet wurde, der für Hochtemperaturanwendungen völlig ungeeignet war.
Die erste Aufgabe von Bosch war die Entwicklung eines neuen Laborreaktors, für den er Habers ursprüngliche Konstruktion zu einem robusten, zuverlässigen Reaktor ummodellierte. 24 Beispiele liefen mehrere Jahre rund um die Uhr, während Mittasch nach dem perfekten Katalysator suchte.,
Die kleinen Reaktionskammern hatten keines der Probleme, die Bosch beim Scale-up zu bewältigen hatte: Die äußeren drucktragenden Teile waren so klein, dass die Luftkühlung ausreichte, um sie stabil zu halten, und die inneren Teile wurden nur geringfügig mechanisch beansprucht.
„Dieser Zustand sollte sich bald ändern, als wir begannen, einen kleineren Konverter als Produktionsgerät zu bauen“, sagte Bosch. Als Haber einen ähnlichen Versuch unternommen hatte, scheiterte das Gerät nach nur wenigen Betriebsstunden, so dass das Team von Bosch ein sehr stabiles, extern beheiztes Kontaktrohr als Reaktionskammer entwarf., Trotzdem gingen sie kein Risiko ein: „Vorsichtig hatten wir es in einer starken Stahlbetonkammer fernab von allen geschäftigen Tätigkeitszentren untergebracht, da wir uns in der Zwischenzeit auch mit der Gefahr von Bränden und Rückschlägen vertraut gemacht hatten, die häufig bei spontaner Zündung auftreten, wenn Wasserstoff unter hohem Druck austritt“, sagte er.
Es war eine kluge Vorsichtsmaßnahme: Nach 80 Betriebsstunden wurde das Material spröde und die Rohre platzten. Es stellte sich heraus, dass der Wasserstoff das Perlit im Kohlenstoffstahl dekarbonisiert und mit dem Eisen eine spröde Legierung gebildet hatte.,
Bosch löste das Problem, indem es die erste ausgekleidete Reaktionskammer entwarf – einen druckführenden Stahlmantel, der dünn mit einem weichen Stahl ausgekleidet war. Wasserstoff konnte durch die Auskleidung diffundieren und durfte durch Rillen und Löcher im Mantel entweichen, um einen gefährlichen Druckaufbau zu verhindern.
„Die Lösung erschien einfach und war tatsächlich so, aber die gesamte Entwicklung des Prozesses hing mehr oder weniger davon ab“, sagte Bosch.,
Sicherheitsüberlegungen
Nicht, dass dies das letzte Problem von Bosch gewesen wäre: Der Wärmetauscher war zu ineffizient, die druckführenden Stahljacken neigten nach längerem Betrieb immer noch dazu, sich zu wölben und zu explodieren-ein Problem, das erst überwunden wurde, als Bosch, im Bruch mit der damaligen Konvention, versuchte, den Reaktor von innen zu erwärmen – und Kompressoren, die unzuverlässig waren und dazu neigten, auszulaufen. Dies stellt ein inakzeptables Risiko dar, wenn das austretende Gas Wasserstoff ist; ganz zu schweigen davon, dass keine chemische Anlage mit Kompressoren arbeiten kann, die mindestens einmal am Tag ausfallen.,
Das Team von Bosch baute nicht nur eigene Kompressoren, es musste auch eigene Überwachungsinstrumente entwickeln und produzieren, um Temperatur, Intensität des Gasstroms und die Zusammensetzung des Gases in der Reaktionskammer zu messen – Standardgeräte 20 Jahre später, aber unbekannt, als Bosch Habers Gerät skalierte.
Bosch war sich auch der Gesundheit und Sicherheit sehr bewusst und entwarf zahlreiche schnell wirkende Sicherheitsventile und andere Geräte, so dass die Anlage mit Rekordgeschwindigkeit heruntergefahren und evakuiert werden konnte., „Im Laufe der Jahre konnten wir genügend Erfahrung sammeln, insbesondere während des Krieges, als die Oppau-Werke Nacht für Nacht bombardiert wurden, und wir sind immer noch der Meinung, dass man nicht zu vorsichtig sein kann“, sagte er.
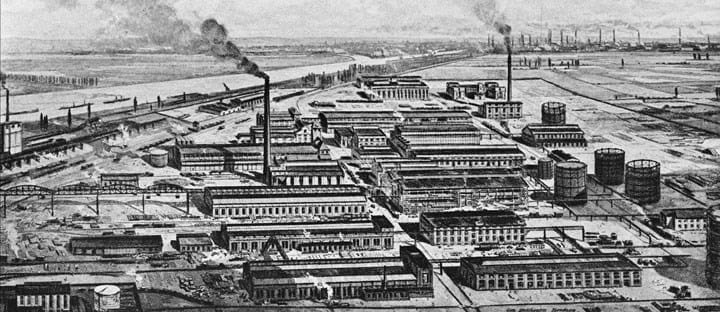
Nature knows best
Die erste Anlage, die das Haber-Bosch-Verfahren im industriellen Maßstab einsetzte, wurde 1913 bei BASF Oppau eröffnet. Fast 100 Jahre auf nichts viel hat sich geändert, und der Prozess wird immer noch auf der ganzen Welt verwendet.,
Haber sagte jedoch voraus, dass sich das ändern würde: „Stickstoffbakterien lehren uns, dass die Natur mit ihren ausgeklügelten Formen der Chemie lebender Materie immer noch Methoden versteht und anwendet, die wir noch nicht imitieren können. Es genügt, dass inzwischen eine verbesserte Stickstoffdüngung des Bodens der Menschheit neue nährstoffreiche Reichtümer bringt und dass die chemische Industrie dem Bauern zu Hilfe kommt, der in der guten Erde Steine in Brot verwandelt.“
Ursprünglich im März 2010 veröffentlicht
Schreibe einen Kommentar