Claudia Flavell-podczas gdy profile działań zmieniających świat Fritz Haber i Carl Bosch
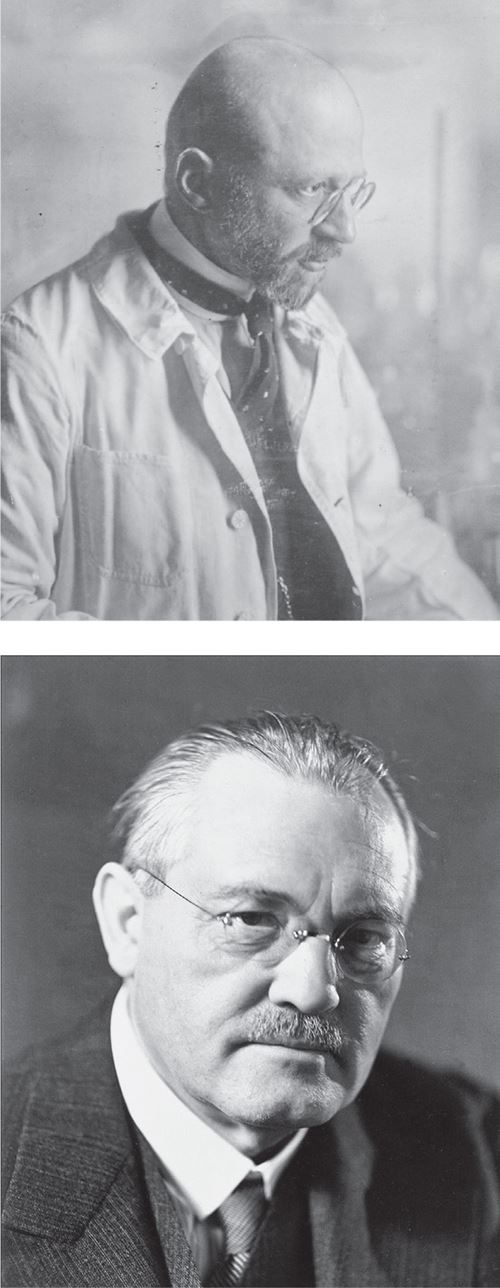
żaden wyczyn Inżynierii Chemicznej nie ilustruje bardziej obosiecznego charakteru wielu wynalazków niż proces haber-Bosch., Opracowany przez chemika przemysłowego Fritza Habera i skalowany przez inżyniera chemika Carla Boscha, proces Haber-Bosch pobiera azot z powietrza i zamienia go w amoniak.
pozwoliło to po raz pierwszy produkować nawozy syntetyczne i produkować wystarczającą ilość żywności dla rosnącej populacji Ziemi. Rzeczywiście, bez procesu Haber-Bosch moglibyśmy wyprodukować tylko około dwóch trzecich ilości żywności, którą obecnie produkujemy, a ludność Ziemi musiałaby się odpowiednio zmniejszyć.,
azot jest również kluczowym surowcem w produkcji materiałów wybuchowych. Kiedy Niemcy wyczerpały zapasy naturalnego amoniaku we wczesnych etapach I wojny światowej, syntetyczny amoniak był tam, aby wypełnić lukę. Bez procesu Habera-Boscha I wojna światowa byłaby znacznie krótsza.
Haber, wytrawny patriota, zyskał później rozgłos dzięki pracy nad wykorzystaniem chemikaliów na korzyść Niemiec w I Wojnie Światowej, a on osobiście nadzorował i kierował pierwszym na dużą skalę uwalnianiem chloru w Ypres w 1915 roku.,
zapobieganie głodowi
jednak to właśnie proces Habera-Boscha i jego wkład w żywienie rosnącej populacji świata jest najlepiej pamiętany i słusznie. Wraz z nadejściem epoki przemysłowej i wielkim przeniesieniem się do miast, nawozy były niezbędne do uzupełniania gleby składnikami odżywczymi. Naturalne nawozy, takie jak Guano chilijskie, były ograniczonym zasobem – jeśli nauka nie przyjdzie na ratunek, z pewnością nastąpi głód.
rozwiązanie problemu przyniosło Haberowi i Boschowi dwie Nagrody Nobla w dziedzinie chemii: Haber w 1918 roku, Bosch w 1931 roku.,
problem z azotem polega na tym, że chociaż jest on obfity w atmosferze, jego potrójne wiązania sprawiają, że cząsteczka azotu jest niewiarygodnie stabilna, a zatem trudna do naprawienia. Haber należał do grupy chemików, do których należeli również Walther Nernst i Henry Le Chatelier, którzy postanowili rozwiązać ten problem.,
bez procesu Haber-Bosch moglibyśmy wyprodukować tylko około dwóch trzecich ilości żywności, którą obecnie produkujemy
ścieżki i ślepe alejki
Haber początkowo próbował produkować tlenek azotu za pomocą wyładowań elektrycznych, naśladując naturalne procesy podczas burzy. Ale wydajność była tak niska, a proces tak uciążliwy, że Haber odrzucił go jako niepraktyczny.
Haber następnie badał syntezę wysokotemperaturową, z pewnym sukcesem, a nawet udało mu się wyprodukować niewielką ilość azotu w 1905 roku., Ale był rozczarowany wydajnością 5%, w temperaturze około 1000ºC. Potrzebne były lepsze katalizatory lub wyższe ciśnienie, ale synteza wysokociśnieniowa była w powijakach i brakowało odpowiedniego sprzętu. Rzeczywiście, Le Chatelier, który jako pierwszy zasugerował mocowanie azotu pod wysokim ciśnieniem, zrezygnował po szczególnie silnej eksplozji laboratoryjnej.
dopiero w 1908 roku Haber, współpracując ze swoim uczniem Robertem Le Rossignolem, postanowił zająć się szlakiem wysokociśnieniowym. To był dobry wybór., Rok później opatentowali proces, w którym otrzymano około 15% amoniaku, działający pod ciśnieniem około 175 atmosfer w temperaturze 550ºC nad katalizatorem osmu i uranu.
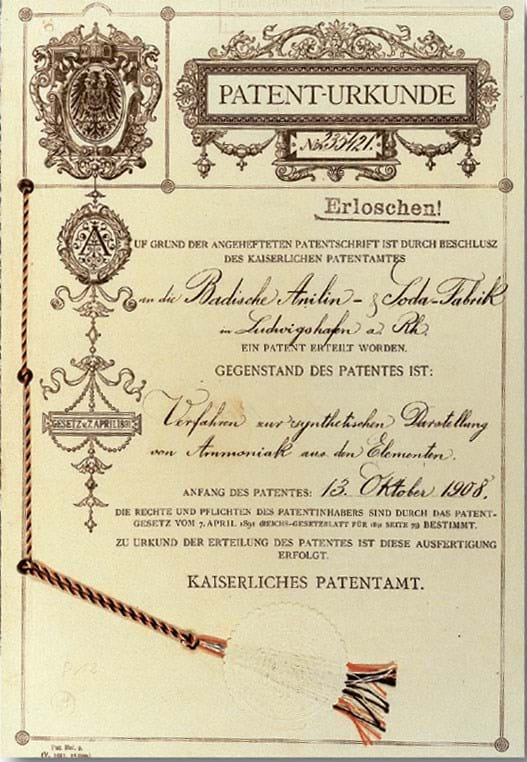
od laboratorium do przemysłu
proces został wkrótce przypisany do Badische Anilin und Soda Fabrik (lepiej znany dziś pod skrótem BASF), który zlecił inżynierowi chemicznemu Carlowi Bosch skalowanie w górę proces., Bosch powiedział później: „było oczywiste, że istnieją trzy główne problemy, które musiały zostać rozwiązane przed rozpoczęciem budowy zakładu. Były to dostawy surowców, tj. gazów wodór i azot, po niższej niż dotychczas cenie; produkcja skutecznych i stabilnych katalizatorów; i wreszcie Budowa aparatury.,”
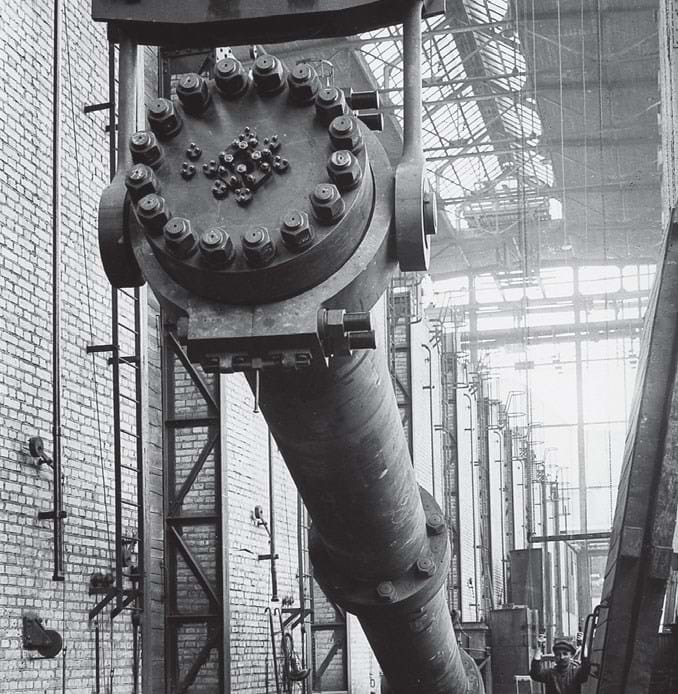
tani i wesoły
proces produkcji wodoru przez elektrolizę Habera nie pozwolił na zwiększenie skali. Podobnie jak inne znane procesy produkcji wodoru, które były albo zbyt drogie, albo wytwarzały Wodór ze zbyt dużą ilością zanieczyszczeń.
Bosch i jego zespół ostatecznie zdecydowali się na gaz wodny-gaz syntezowy składający się z wodoru i tlenku węgla – jako jedyne praktyczne rozwiązanie., Firma pozyskała czysty Wodór przy użyciu niedawno opracowanego procesu Linde-Frank-Caro, który chłodzi Gaz Wodny w kilku krokach do-205ºC, w którym wszystkie elementy oprócz skroplenia wodoru.
drugim istotnym wkładem było zastąpienie katalizatora osmu uranowego bardziej praktyczną alternatywą. OSM nie nadawał się do skalowania, ponieważ światowe zapasy wynosiły zaledwie kilka kilogramów, a uran był drogi i bardzo wrażliwy na wodę i tlen. Potrzeba było asystenta Boscha, chemika Alwina Mittascha, około 20 000 eksperymentów, aby udoskonalić mieszany katalizator oparty na tlenku żelaza., Był to pierwszy w swoim rodzaju i występował zarówno jako OSM, jak i uran, był łatwo dostępny i tani. Katalizator jest nadal używany do dziś, a Mittasch jest pamiętany jako jeden z wielkich pionierów chemii katalitycznej.
zbiorniki ciśnieniowe
Bosch uważa, że jego największym wyczynem było rozwiązanie trzeciego problemu, jak zbudować reaktor, który wytrzymałby zarówno wysokie temperatury, jak i wysokie ciśnienie reakcji. Chemia wysokociśnieniowa była wciąż bardzo nową dziedziną, a odpowiedniego sprzętu brakowało., Jedynym istniejącym procesem wysokociśnieniowym był proces skraplania powietrza Linde, proces niskotemperaturowy, w którym zastosowano miękki lutowany reaktor miedziany, który był całkowicie nieodpowiedni do zastosowań w wysokich temperaturach.
pierwszym zadaniem Boscha było opracowanie nowego reaktora laboratoryjnego, dla którego przebudował oryginalny projekt Habera w solidny i niezawodny reaktor. Około 24 przykładów działało przez całą dobę przez kilka lat, podczas gdy Mittasch szukał idealnego katalizatora.,
małe Komory reakcyjne nie miały żadnego z problemów, z jakimi borykał się Bosch w skalowaniu: zewnętrzne części ciśnieniowe były na tyle małe, że chłodzenie powietrzem było wystarczające, aby utrzymać ich stabilność, a wewnętrzne części były tylko lekko naprężone mechanicznie.
„Ten stan rzeczy wkrótce się zmienił, gdy zaczęliśmy budować mniejszy konwerter jako aparat produkcyjny”, powiedział Bosch. Kiedy Haber podjął podobną próbę, urządzenie zawiodło po zaledwie kilku godzinach pracy, więc zespół Bosch zaprojektował bardzo wytrzymałą, ogrzewaną zewnętrznie rurę kontaktową jako komorę reakcyjną., Mimo to nie zaryzykowali: „zachowując ostrożność, trzymaliśmy go w silnej, żelbetowej komorze z dala od wszystkich ruchliwych ośrodków aktywności, ponieważ w międzyczasie zaznajomiliśmy się również z niebezpieczeństwem pożarów i wybuchów, które występują, często przy samozapłonie, gdy Wodór wyłania się pod wysokim ciśnieniem” – powiedział.
To był mądry środek ostrożności: po 80 godzinach pracy materiał stał się kruchy, a rury pękły. Okazało się, że wodór dekarbonizował perlit w stali węglowej i utworzył kruchy stop z żelazem.,
firma Bosch rozwiązała ten problem, projektując pierwszą komorę reakcyjną z podszewką-stalową płaszczem ciśnieniowym cienko wyłożoną miękką stalą. Wodór był w stanie rozproszyć się przez podszewkę i mógł uciec przez rowki i otwory w płaszczu, aby zapobiec niebezpiecznemu gromadzeniu się ciśnienia.
„rozwiązanie wydawało się proste i w rzeczywistości tak było, ale cały rozwój procesu zależał od niego w mniejszym lub większym stopniu” – powiedział Bosch.,
względy bezpieczeństwa
nie chodzi o to, że był to ostatni z problemów firmy Bosch: wymiennik ciepła był zbyt nieefektywny, stalowe Płaszcze ciśnieniowe nadal miały tendencję do zapinania się i eksplodowania po dłuższej pracy-problem został rozwiązany tylko wtedy, gdy Bosch, zrywając z konwencją czasów, próbował podgrzać reaktor od wewnątrz – i sprężarki, które były zawodne i miały tendencję do wycieku. Stwarza to niedopuszczalne ryzyko, gdy wyciekającym gazem jest wodór; nie wspominając o tym, że żadna instalacja chemiczna nie może pracować ze sprężarkami, które zawodzą co najmniej raz dziennie.,
zespół Bosch nie tylko budował własne sprężarki, ale także projektował i produkował własne przyrządy monitorujące do pomiaru temperatury, natężenia strumienia gazu i składu gazu w komorze reakcyjnej – urządzenia dostępne od 20 lat, ale niespotykane, gdy Bosch powiększył urządzenie Habera.
firma Bosch była również bardzo świadoma kwestii bezpieczeństwa i Higieny Pracy i zaprojektowała liczne szybko działające zawory bezpieczeństwa i inne urządzenia, dzięki czemu zakład mógł zostać wyłączony i ewakuowany z rekordową prędkością., „Przez lata udało nam się zdobyć wystarczające doświadczenie, zwłaszcza w czasie wojny, kiedy nocą bombardowano zakłady Oppau, i nadal jesteśmy zdania, że nie można być zbyt ostrożnym” – powiedział.
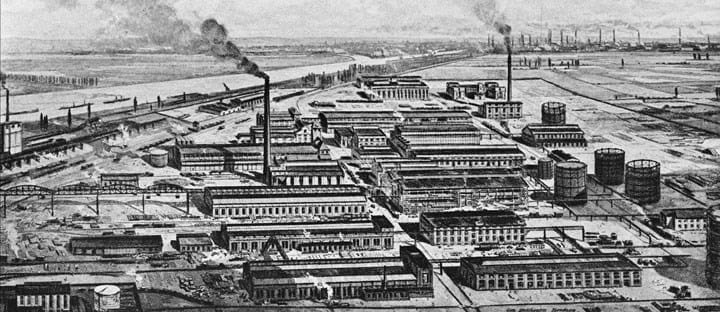
natura wie najlepiej
pierwsza instalacja wykorzystująca proces Haber-Bosch na skalę przemysłową rozpoczęła działalność w BASF Oppau w 1913 roku. Prawie 100 lat nic się nie zmieniło, a proces ten jest nadal używany na całym świecie.,
jednak Haber przewidział, że to się zmieni: „bakterie azotowe uczą nas, że natura, dzięki swoim wyrafinowanym formom chemii żywej materii, nadal rozumie i wykorzystuje metody, których jeszcze nie wiemy, jak naśladować. Wystarczy, że w międzyczasie udoskonalone azotowe nawożenie gleby przynosi ludzkości nowe bogactwa odżywcze, a przemysł chemiczny przychodzi z pomocą rolnikowi, który na dobrej ziemi zamienia kamienie w chleb.”
Dodaj komentarz