Claudia Flavell-Mentre i profili di cambiare il mondo, gli sforzi di Fritz Haber e Carl Bosch
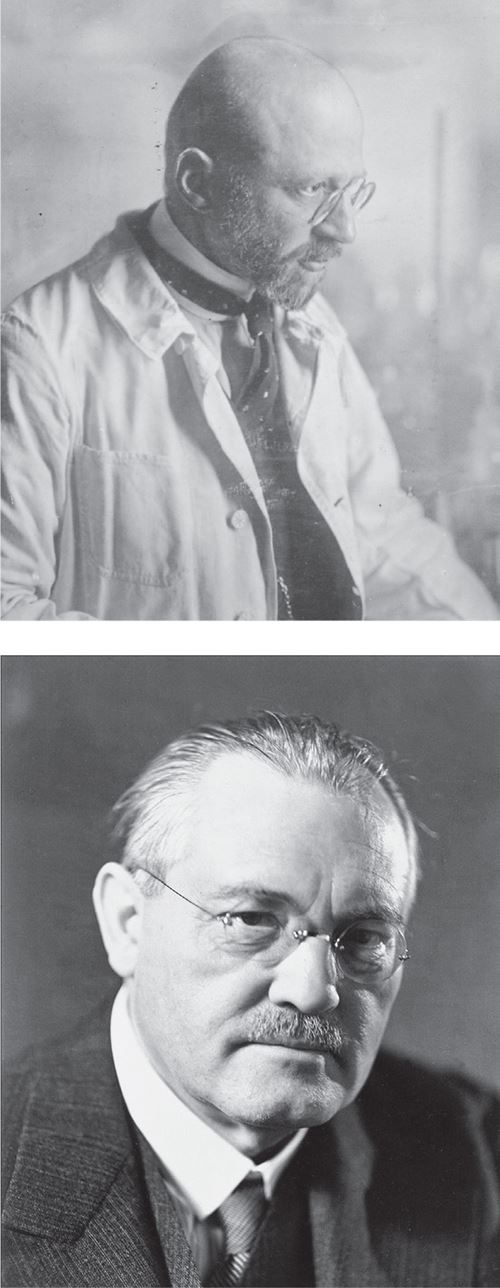
Nessun ingegneria chimica feat illustra meglio il doppio taglio della natura di molte invenzioni di Haber-Bosch processo., Sviluppato dal chimico industriale Fritz Haber e ridimensionato dall’ingegnere chimico Carl Bosch, il processo Haber-Bosch prende l’azoto dall’aria e lo converte in ammoniaca.
Ciò ha permesso per la prima volta di produrre fertilizzanti sintetici e produrre cibo sufficiente per la crescente popolazione della Terra. In effetti, senza il processo Haber-Bosch saremmo in grado di produrre solo circa due terzi della quantità di cibo che facciamo oggi, e la popolazione della Terra dovrebbe ridursi di conseguenza.,
Sul rovescio della medaglia, l’azoto è anche una materia prima chiave nella produzione di esplosivi ad alto potenziale. Quando la Germania esaurì le sue forniture di ammoniaca naturale nelle prime fasi della prima guerra mondiale, l’ammoniaca sintetica era lì per colmare il divario. Senza il processo Haber-Bosch, la prima guerra mondiale sarebbe stata notevolmente più breve.
Haber, un patriota consumato, avrebbe poi acquisito notorietà attraverso il suo lavoro sull’uso di sostanze chimiche a vantaggio della Germania nella prima guerra mondiale, e supervisionò personalmente e diresse il primo rilascio su larga scala di gas cloro a Ypres nel 1915.,
Evitare la carestia
Tuttavia, è il processo Haber-Bosch e il suo contributo all’alimentazione della crescente popolazione mondiale per cui è ricordato, e giustamente. Con l’avvento dell’era industriale e il grande trasferimento nelle città, i fertilizzanti erano essenziali per riempire il terreno con sostanze nutritive. Concimi naturali come il guano cileno erano una risorsa limitata-se la scienza non è venuto in soccorso, carestia era certo a seguire.
Risolvere il problema valse a Haber e Bosch due premi Nobel per la chimica: Haber nel 1918, Bosch nel 1931.,
Il problema con l’azoto è che, mentre è abbondante nell’atmosfera, i suoi tripli legami rendono la molecola di azoto incredibilmente stabile e quindi difficile da risolvere. Haber era uno di un gruppo di chimici che comprendeva anche Walther Nernst e Henry Le Chatelier, che aveva deciso di affrontare il problema.,
Senza Haber-Bosch processo ci sarebbe solo in grado di produrre circa due terzi la quantità di cibo che abbiamo noi oggi
Vie e vicoli ciechi
Haber inizialmente tentato di produrre ossido nitrico, con l’aiuto di scariche elettriche, imitando i processi naturali, durante un temporale. Ma la resa era così bassa e il processo così oneroso che Haber ha respinto come impraticabile.
Haber successivamente studiò la sintesi ad alta temperatura, con un certo successo, e riuscì persino a produrre una piccola quantità di azoto nel 1905., Ma era deluso dalla resa del 5%, a temperature di circa 1000ºC. Erano necessari catalizzatori migliori o pressioni più elevate, ma la sintesi ad alta pressione era agli inizi e le attrezzature adeguate scarseggiavano. In effetti, Le Chatelier, che fu il primo a suggerire di fissare l’azoto ad alta pressione, rinunciò dopo un’esplosione di laboratorio particolarmente pesante.
Fu solo nel 1908 che Haber, lavorando con il suo allievo Robert le Rossignol, decise di affrontare la via dell’alta pressione. E ‘ stata una buona scelta., Un anno dopo, hanno brevettato un processo che ha prodotto circa il 15% di ammoniaca, operando ad una pressione di circa 175 atmosfere a 550ºC su un catalizzatore di osmio e uranio.
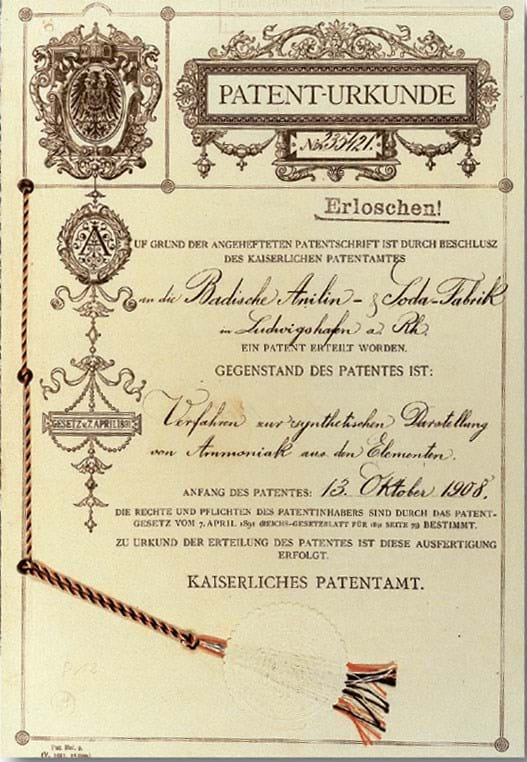
Dal laboratorio all’industria
Il processo è stato subito assegnato a Badische Anilin und Soda Fabrik (meglio conosciuta oggi con la sua sigla, BASF), che il compito ingegnere chimico Carl Bosch con il ridimensionamento il processo., Bosch in seguito disse: “Era ovvio che c’erano tre problemi principali che dovevano necessariamente essere risolti prima che la costruzione di un impianto potesse essere intrapresa. Questi sono stati fornitura di materie prime, vale a dire dei gas idrogeno e azoto, ad un prezzo inferiore a quello finora possibile; la fabbricazione di catalizzatori efficaci e stabili; e infine la costruzione degli apparecchi.,”
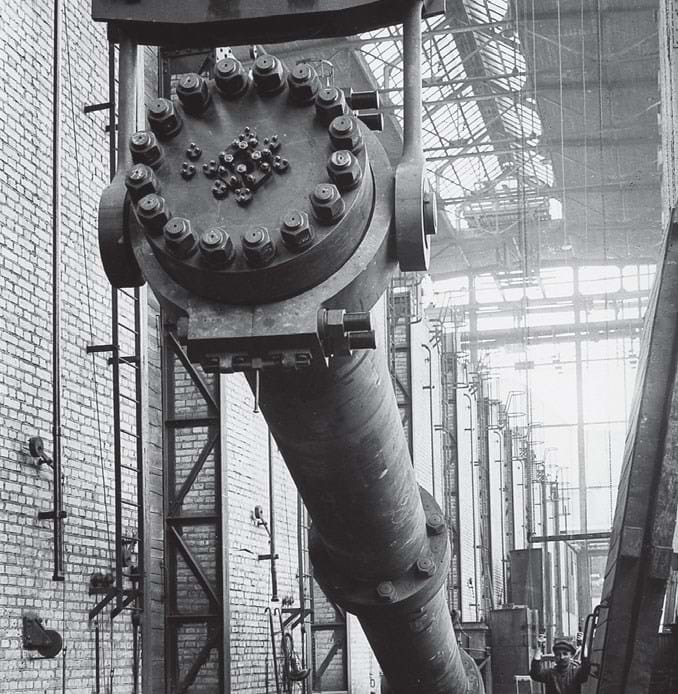
Economico e allegro
Il processo di produzione di idrogeno da parte di Haber per elettrolisi non si prestava allo scale-up. Né ha fatto nessuno degli altri processi di produzione di idrogeno noti, che erano troppo costosi o prodotto idrogeno con troppe impurità.
Bosch e il suo team alla fine si stabilirono sull’acqua-gas – un gas di sintesi costituito da idrogeno e monossido di carbonio – come unica soluzione pratica., L’azienda ha estratto l’idrogeno puro utilizzando il processo Linde-Frank-Caro di recente sviluppo, che raffredda il gas dell’acqua in diversi passaggi fino a-205ºC, a quel punto tutti gli elementi tranne l’idrogeno si liquefanno.
Il secondo importante contributo è stato sostituire il catalizzatore di osmio dell’uranio con un’alternativa più pratica. L’osmio non era adatto per lo scale up perché le forniture globali ammontavano a pochi chilogrammi e l’uranio era costoso e molto sensibile all’acqua e all’ossigeno. L’assistente di Bosch, il chimico Alwin Mittasch, impiegò circa 20.000 esperimenti per perfezionare un catalizzatore misto a base di ossido di ferro., E ‘ stato il primo del suo genere, ed eseguito così come osmio e uranio, ed era prontamente disponibile ed economico. Il catalizzatore è ancora in uso oggi e Mittasch è ricordato come uno dei grandi pionieri della chimica catalitica.
Recipienti a pressione
Bosch ritiene che la sua più grande impresa è stata risolvere il terzo problema, come costruire un reattore che avrebbe resistito sia alle alte temperature e alte pressioni della reazione. La chimica ad alta pressione era ancora un campo molto nuovo e le attrezzature adeguate scarseggiavano., L’unico processo ad alta pressione esistente era il processo di liquefazione dell’aria di Linde, un processo a bassa temperatura che utilizzava un reattore di rame saldato morbido che era del tutto inadatto per applicazioni ad alta temperatura.
Il primo compito di Bosch fu quello di ideare un nuovo reattore da laboratorio, per il quale ri-modellò il progetto originale di Haber in un reattore robusto e affidabile. Alcuni esempi 24 correvano tutto il giorno per diversi anni mentre Mittasch cercava il catalizzatore perfetto.,
Le piccole camere di reazione non avevano nessuno dei problemi che Bosch doveva incontrare nello scale-up: le parti esterne portanti la pressione erano abbastanza piccole che il raffreddamento ad aria era sufficiente per mantenerle stabili, e c’era solo una leggera sollecitazione meccanica sulle parti interne.
“Questo stato di cose doveva presto cambiare quando abbiamo iniziato a costruire un convertitore più piccolo come apparato di produzione”, ha detto Bosch. Quando Haber aveva fatto un tentativo simile, il dispositivo fallì dopo solo un paio d’ore di funzionamento, quindi il team di Bosch progettò un tubo di contatto molto robusto e riscaldato esternamente come camera di reazione., Anche così, non hanno preso rischi: “Essendo cauti, l’avevamo ospitato in una camera di cemento armato forte e lontana da tutti i centri di attività, poiché nel frattempo avevamo anche preso confidenza con il pericolo di incendi e flarebacks che si verificano, spesso con l’accensione spontanea, quando l’idrogeno emerge ad alta pressione”, ha detto.
Era una saggia precauzione: dopo 80 ore di servizio, il materiale diventava fragile e i tubi scoppiavano. Si è scoperto che l’idrogeno aveva decarbonizzato la perlite nell’acciaio al carbonio e formato una lega fragile con il ferro.,
Bosch ha risolto il problema progettando la prima camera di reazione foderata: una camicia in acciaio a pressione rivestita sottilmente con un acciaio morbido. L’idrogeno è stato in grado di diffondersi attraverso il rivestimento ed è stato permesso di fuoriuscire attraverso scanalature e fori nella giacca, per evitare un pericoloso accumulo di pressione.
“La soluzione sembrava semplice e lo era in effetti, ma l’intero sviluppo del processo dipendeva da esso in misura maggiore o minore”, ha affermato Bosch.,
considerazioni di Sicurezza
Non che questo era l’ultimo di Bosch problemi: lo scambiatore di calore è troppo inefficiente, la pressione in acciaio del cuscinetto giacche tendeva ancora a fibbia e esplodere dopo un funzionamento prolungato – un problema solo superare quando Bosch, in un momento di pausa con la convenzione dei tempi, ha cercato il riscaldamento del reattore dall’interno e compressori che sono inaffidabili e tendevano a perdere. Ciò comporta un rischio inaccettabile quando il gas che fuoriesce è idrogeno; per non parlare del fatto che nessun impianto chimico può funzionare con compressori che falliscono almeno una volta al giorno.,
Il team Bosch non solo ha costruito i propri compressori, ma ha anche dovuto progettare e produrre i propri strumenti di monitoraggio per misurare la temperatura, l’intensità del flusso di gas e la composizione del gas nella camera di reazione – dispositivi off-the-shelf 20 anni dopo, ma inaudito quando Bosch ha scalato il dispositivo di Haber.
Bosch era anche molto consapevole della salute e della sicurezza, e ha progettato numerose valvole di sicurezza ad azione rapida e altre attrezzature in modo che l’impianto potesse essere spento ed evacuato con velocità record., “Nel corso degli anni siamo stati in grado di raccogliere sufficiente esperienza, soprattutto durante la guerra, quando le opere Oppau sono stati bombardati notte dopo notte, e siamo ancora oggi del parere che non si può essere troppo attenti,” ha detto.
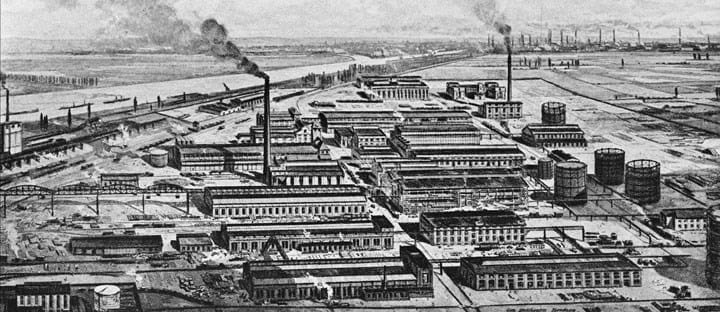
Nature knows best
Il primo impianto ad utilizzare il processo Haber-Bosch su scala industriale fu avviato a BASF Oppau nel 1913. Quasi 100 anni su nulla è cambiato molto, e il processo è ancora utilizzato in tutto il mondo.,
Tuttavia, Haber predisse che questo sarebbe cambiato: “I batteri dell’azoto ci insegnano che la Natura, con le sue forme sofisticate della chimica della materia vivente, comprende e utilizza ancora metodi che non sappiamo ancora imitare. Basti pensare che nel frattempo una migliore concimazione azotata del suolo porta nuove ricchezze nutritive all’umanità e che l’industria chimica viene in aiuto del contadino che, nella buona terra, trasforma le pietre in pane.”
Originariamente pubblicato nel marzo 2010
Lascia un commento